A palletizer is a device specifically designed for the automated palletizing of steel products (such as steel plates, steel pipes, section steel, etc.). Its main working objective is to stack steel products on pallets or other loading devices in a predetermined manner (such as neat stacking, specific arrangement patterns), facilitating the storage, transportation, and subsequent processing of steel.
Electromagnetic Suction Cup: For flat steel products like steel plates, the electromagnetic suction cup is a commonly used gripping tool. It utilizes the electromagnetic principle. When energized, it generates a strong magnetic force to adsorb steel, enabling it to effectively grip relatively heavy steel plates. For example, in large steel plate processing enterprises, the electromagnetic suction cup can stably grip steel plates with thicknesses ranging from a few millimeters to several tens of millimeters. Its suction force can withstand the weight of steel plates weighing several tons. Moreover, the suction force of the electromagnetic suction cup can be controlled by adjusting the current to adapt to steel plates of different weights and sizes.
Chain Conveyor Mechanism: This type of conveying mechanism is suitable for heavier steel products, such as large section steel. It transports steel through the movement of a chain. The chain is usually made of high-strength alloy steel and can bear a large amount of weight and friction. Additionally, the chain conveyor mechanism can be set to different conveying speeds as needed to match the working rhythm of the palletizer.
Roller Conveyor Mechanism: For steel products with relatively flat surfaces, such as steel plates and cylindrical steel pipes, the roller conveyor mechanism is an excellent choice. It consists of a series of parallel rollers. Steel products are placed on the rollers, and the rotation of the rollers realizes the transportation of steel. The advantages of the roller conveyor mechanism are low friction, high conveying speed, and easy connection with other production equipment or warehousing facilities. For example, in a steel plate production workshop, the roller conveyor mechanism can directly transport cut steel plates to the gripping position of the palletizer.
Control System
The control system of the palletizer in the steel industry is usually based on a PLC (Programmable Logic Controller) or a Computer Numerical Control (CNC) system. The PLC system can precisely control the action sequence, speed, and position of each component of the palletizer. Operators can set parameters such as the palletizing pattern (such as the rectangular pattern, staggered pattern, etc.), the quantity of steel per layer, and the number of stacking layers through programming. For example, during the palletizing process of section steel, the PLC system can accurately calculate the stacking position of each piece of section steel according to its length, width, and palletizing requirements, ensuring the neatness and stability of the palletizing. At the same time, the control system can communicate and interact with other equipment on the steel production line to realize the automation of the entire production process.
Characteristics of the Workflow
Steel Feeding: Steel enters the working area of the palletizer from the production line (such as the steel rolling production line, steel pipe production line, etc.) through the conveying system. During the feeding process, sensors will detect information such as the size, shape, position, and speed of the steel and feedback this information to the control system. For example, when a steel pipe enters the working area of the palletizer, a photoelectric sensor will detect its arrival and send a signal to the control system. The control system will then control the speed of the conveying system according to the signal to ensure that the steel pipe enters the gripping position at an appropriate speed.
Steel Gripping and Positioning: According to the type of steel, the gripping device will grip the steel under the command of the control system. During the gripping process, the control system will fine-tune the gripping device according to the steel position information fed back by the sensors to ensure accurate gripping. For example, when an electromagnetic suction cup grips a steel plate, a position sensor will detect the distance and relative position between the suction cup and the steel plate. The control system will adjust the position of the suction cup to enable it to precisely adsorb at the center of the steel plate or at the preset gripping points.
Palletizing and Stacking: The gripped steel is transported to the designated position above the pallet for stacking. During the stacking process, the control system will operate strictly in accordance with the preset palletizing pattern. In the steel industry, due to the heavy weight of steel, a relatively stable palletizing pattern is usually adopted, such as the rectangular pattern. In the rectangular pattern, the steel is neatly arranged in rows and columns. The spacing between each row and column can be set according to the size of the steel and the size of the pallet. For example, when palletizing steel plates, the control system will control the robotic arm to place the steel plates one by one on the pallet in a rectangular pattern, ensuring the flatness and alignment between each layer of steel plates to increase the stability of the stack.
Pallet Handling: After a layer of steel is stacked, the pallet will move according to the instructions of the control system (such as through a pallet conveying device) to prepare for the stacking of the next layer of steel. Some palletizers can also automatically replace pallets. When a pallet is fully stacked, it will be transported to the designated storage or transportation area, and at the same time, a new pallet will be introduced for the next round of palletizing.
Application Scenarios and Advantages
Application Scenarios
Steel Plate Processing Enterprises: It is used to palletize cut steel plates according to the size and quantity required by customers, facilitating the sales and transportation of steel plates. For example, in a construction steel plate production enterprise, the palletizer can stack steel plates of different thicknesses and specifications on pallets. The number of steel plates on each pallet and their arrangement pattern meet the construction requirements of construction enterprises.
Steel Pipe Production Enterprises: At the final stage of steel pipe production, the palletizer can palletize finished steel pipes according to a certain length, diameter, and quantity. This is very important for the warehousing management and batch transportation of steel pipes. For example, in an oil pipeline production enterprise, after the palletizer has palletized the steel pipes, it is convenient to use a forklift to move the pallets to the warehouse or transportation vehicles.
Section Steel Manufacturers: For various types of section steel (such as I-beams, channel steel, etc.), the palletizer can stack them neatly on pallets, facilitating the storage and subsequent processing of section steel. For example, in a steel structure manufacturing enterprise, the section steel palletizer can stack the section steel according to the requirements of the processing order and directly supply it to the production line, reducing the workload of manual handling and sorting.
Advantages
Improved Efficiency: The palletizer in the steel industry can carry out palletizing operations quickly and continuously, greatly increasing the palletizing speed of steel. Compared with manual palletizing, its efficiency can be increased several times or even dozens of times. For example, in a large steel plate production plant, manual palletizing may only be able to complete the palletizing task of a few tons of steel plates per hour, while the palletizer can complete the palletizing of dozens of tons or even hundreds of tons of steel plates per hour.
Quality Assurance: The palletizer can ensure the accuracy and stability of steel palletizing. Due to the heavy weight and regular shape of steel, through the precise control system and appropriate gripping and conveying devices, the palletizer can stack the steel neatly on the pallet, avoiding problems such as uneven placement and unstable stacking that may occur in manual palletizing. For example, during the palletizing process of steel pipes, the palletizer can keep each layer of steel pipes horizontal and aligned with each other, improving the quality of the stack.
Cost Reduction: On the one hand, it reduces labor costs. In the labor-intensive and relatively harsh working environment of steel palletizing, the use of a palletizer can significantly reduce the labor input. On the other hand, it reduces the loss of steel during the palletizing process. Due to the precise operation of the palletizer, the damage to steel caused by collisions, drops, etc. is reduced, thereby reducing the loss cost of the enterprise.
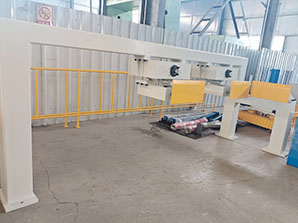