I. Product Overview
The steel palletizer is an automated device specifically developed and designed for the production, processing, and warehousing of steel. It aims to achieve efficient and precise palletizing of steel, significantly improve production efficiency, reduce labor costs, and ensure the quality and safety of palletizing. It integrates advanced technologies such as mechanical manufacturing, electrical control, and automated sensing, and is an indispensable and important piece of equipment in the modern steel industry.
II. Working Principle
Steel Conveying and Positioning: Steel is smoothly conveyed to the grabbing position of the palletizer through equipment such as conveying roller tables or chain conveyors. During the conveying process, sensors will conduct real-time detection and feedback of parameters such as the position, size, and shape of the steel to ensure that the steel can reach the designated position accurately, preparing for the subsequent grabbing action.
Grabbing and Handling: The grabbing mechanism of the palletizer usually uses methods such as electromagnet suction and mechanical fixture clamping to grab the steel. Taking electromagnet suction as an example, when the steel reaches the designated position, the electromagnet is energized to generate a strong magnetic force, firmly attracting the steel. Subsequently, the transmission system composed of motors, reducers, lead screw guides, etc. drives the grabbing mechanism to transport the steel to the palletizing area according to the preset path and speed.
Palletizing and Stacking: In the palletizing area, the palletizer stacks the steel layer by layer in an orderly manner according to the pre-set palletizing mode, such as the number of steel pieces per layer, the arrangement method, and the number of stacking layers. Through precise position control and action coordination, it is ensured that each layer of steel is neatly arranged and closely fitted to form a stable stack pattern. At the same time, during the palletizing process, the position and posture of the steel will be monitored in real-time, and if there are any deviations, adjustments will be made in a timely manner.
III. Product Structure
Main Frame: It is welded with high-strength steel and undergoes strict tempering and stress-relieving treatment to ensure that the frame structure is stable and has strong rigidity. It can withstand long-term and high-intensity work loads and has good seismic performance to ensure the stability of the palletizer during operation.
Grabbing Mechanism:
Electromagnet Type: It is suitable for adsorbing magnetic steel, such as ordinary carbon steel, low-alloy steel, etc. High-performance electromagnets are used, which have a strong suction force and can quickly adsorb and release the steel. It is equipped with a heat dissipation device to prevent overheating during long-term operation and affect the suction force.
Mechanical Fixture Type: It is designed for non-magnetic steel or steel with special shapes. The fixture is made of high-quality alloy steel and has high hardness and wear resistance after heat treatment. The gripper design conforms to the shape of the steel, enabling firm clamping, and the opening and closing action of the gripper is precisely controlled by a cylinder or motor.
Transmission System:
Horizontal Transmission: Gear and rack transmission or lead screw and nut transmission methods are mostly used. Gear and rack transmission has the characteristics of high transmission efficiency and strong load-bearing capacity, and can achieve fast and smooth horizontal movement; lead screw and nut transmission has higher precision and can meet the demanding positioning accuracy requirements of palletizing tasks.
Vertical Transmission: Chain lifting or wire rope lifting mechanisms are generally selected. Chain lifting has the advantages of simple structure and high reliability; wire rope lifting runs smoothly, has low noise, and can adapt to a large lifting height.
Control System: Taking the Programmable Logic Controller (PLC) as the core, it is combined with the Human-Machine Interface (HMI) for operation and control. The PLC is responsible for receiving sensor signals and precisely controlling the execution elements such as motors and cylinders according to the preset program to achieve the automated operation of the palletizer. The HMI can visually display information such as the equipment operation status, parameter settings, and fault alarms, facilitating operators to monitor and adjust.
Safety Protection System:
Light Curtain Sensor: Light curtains are installed around the working area of the palletizer. When a person or foreign object enters the dangerous area, the light curtain sensor will immediately detect it and send a signal to the control system to make the equipment stop running urgently to avoid collision accidents.
Emergency Stop Button: Multiple emergency stop buttons are set on the operation panel and prominent positions of the equipment. Once an emergency situation occurs, the operator can quickly press the emergency stop button to make the equipment stop all actions immediately.
Safety Fence: A sturdy safety fence is built around the palletizer to effectively isolate the working area from the personnel activity area and prevent personnel from entering the dangerous area by mistake.
IV. Technical Parameters
Palletizing Capacity: It can stack 500 - 1500 pieces of steel per hour. The specific palletizing speed depends on the steel specifications, palletizing mode, and equipment configuration. For example, for small-sized steel of common specifications, the palletizing speed can reach 1000 - 1500 pieces per hour; for large-sized and heavy steel, the palletizing speed is relatively lower, at 500 - 800 pieces per hour.
Applicable Steel Specifications:
Length: It can adapt to steel of different lengths from 1 to 12 meters. By adjusting the stroke range of the conveying mechanism and the grabbing mechanism, various length requirements can be met.
Width: It can handle steel with a width of 50 - 500 mm. For steel of different widths, stable grabbing can be achieved by automatically or manually adjusting the gripper spacing.
Thickness: It can stack steel with a thickness of 2 - 100 mm. For steel of different thicknesses, the suction force or clamping force of the grabbing mechanism can be adjusted accordingly.
Palletizing Accuracy: The positioning accuracy in the horizontal direction can reach ±1 mm, and the positioning accuracy in the vertical direction can reach ±2 mm, ensuring that the steel is neatly stacked and the stack pattern is regular, which is beneficial for subsequent storage and transportation.
Power: The total power of the whole machine is generally between 10 and 30 kilowatts. The specific power depends on factors such as the equipment specifications, motor configuration, and operating conditions. For example, the power of large-sized high-speed palletizers is relatively higher, while the power of small-sized simple palletizers is relatively lower.
Working Air Pressure: If the equipment uses pneumatic components, the working air pressure is usually required to be between 0.5 and 0.8 megapascals. A stable air pressure supply is the key to ensuring the normal operation of the pneumatic components.
V. Product Advantages
Efficient Operation: Compared with manual palletizing, the operation efficiency of the palletizer is greatly improved. It can operate continuously for 24 hours, effectively shortening the production cycle and increasing the production capacity of enterprises. For example, in a production line equipped with a steel palletizer, the daily steel palletizing quantity can be several times higher than that of manual palletizing, which greatly meets the needs of large-scale production.
Improve Palletizing Quality: Through precise program control and advanced sensing technology, the palletizer can stack the steel neatly according to the preset rules, ensuring that each layer of steel is neatly arranged and avoiding the unevenness that may occur in manual palletizing. At the same time, when grabbing and placing the steel, it can accurately control the force and position to ensure that the steel will not shake, slide, etc. during the palletizing process, thus ensuring the stability of the palletizing and reducing the safety risks and the risks of steel damage caused by unstable palletizing.
Reduce Labor Costs: After using the steel palletizer, enterprises can greatly reduce the recruitment and employment of palletizing workers. Generally speaking, a steel production line equipped with a palletizer can reduce 5 - 8 palletizing workers. This not only reduces the labor cost expenditure but also reduces the potential costs brought by personnel management, labor disputes, etc. In addition, the use of the palletizer liberates workers from heavy physical labor, enabling them to engage in more valuable work, such as equipment monitoring, quality inspection, etc., further improving the utilization efficiency of human resources.
Enhance Safety: During the steel palletizing process, there are many safety risks in manual operation, such as being scratched by steel or being injured by falling heavy objects. The steel palletizer can replace manual work in dangerous environments, avoiding workers' direct contact with dangerous items and reducing the probability of work-related injury accidents. At the same time, the palletizer is equipped with a complete set of safety protection devices, such as light curtain sensors, emergency stop buttons, safety fences, etc., which can stop the operation in a timely manner when the equipment has abnormal conditions and provide all-round protection for the safety of operators and equipment.
Improve Space Utilization Rate: The palletizer can formulate the optimal palletizing plan according to the space layout of the warehouse and the size specifications of the steel, stack the steel more compactly, and make full use of the vertical and horizontal space of the warehouse. For example, by reasonably adjusting the palletizing height and arrangement method, the storage capacity of the warehouse can be increased by 30% - 50%, effectively reducing the warehousing costs of enterprises. In addition, for different types and specifications of steel, the palletizer can quickly adapt to the palletizing needs of various steel through simple program adjustment, achieve diversified palletizing operations, and better meet the production and storage needs of enterprises.
VI. Application Scenarios
Steel Production Enterprises: In the hot rolling, cold rolling, section steel and other production lines of steel plants, the steel palletizer can quickly and efficiently palletize various types of steel produced, preparing for the subsequent packaging, storage, and transportation links, and improving the continuity and efficiency of the entire production process.
Steel Processing Enterprises: Such as steel shearing processing centers, steel structure manufacturing enterprises, etc. After processing the steel, the finished steel needs to be palletized and sorted. The steel palletizer can accurately palletize according to the specifications and shapes of the processed steel, facilitating enterprises to manage inventory and deliver goods.
Logistics and Warehousing Centers: In the steel logistics and warehousing links, the palletizer can quickly palletize and store a large number of incoming steel, improving the storage efficiency and space utilization rate of the warehouse. At the same time, when the steel is shipped out, it can also quickly unstack and handle according to the order requirements, improving the overall efficiency of logistics operations.
VII. Maintenance and Upkeep
Daily Maintenance:
Check the appearance of the equipment every day to see if there are any loose, deformed, or damaged parts. If there are any abnormalities, tighten or replace them in a timely manner.
Clean the surface of the equipment and the working area, remove dust, debris, iron filings, etc., keep the equipment clean and tidy, and prevent impurities from entering the interior of the equipment and affecting its normal operation.
Check the lubrication status of each lubrication point, add or replace the lubricating oil in a timely manner to ensure good lubrication of each moving part of the equipment and reduce wear.
Regular Maintenance:
Check the tension and wear of components such as belts, chains, and gears of the transmission system every week, and adjust or replace them if necessary. Check the running sound and temperature of the motor and reducer, and troubleshoot the faults in a timely manner if there are any abnormalities.
Check the control system every month, including PLC program backup, HMI interface function testing, sensor calibration, etc., to ensure the stable operation of the control system.
Check the hydraulic system (if any) of the equipment every quarter, replace the hydraulic oil, clean the filter, and check whether there are any leaks in the hydraulic pipeline to ensure the normal operation of the hydraulic system.
Conduct a comprehensive inspection and maintenance of the equipment every year, including flaw detection of the mechanical structure, aging test of electrical components, accuracy calibration of the equipment, etc., to ensure that the equipment can still maintain good performance and accuracy after long-term operation.
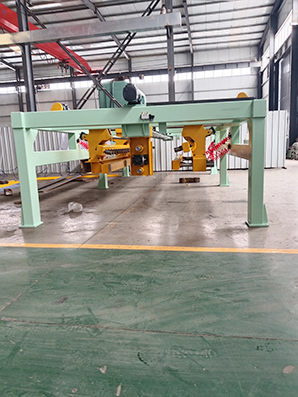
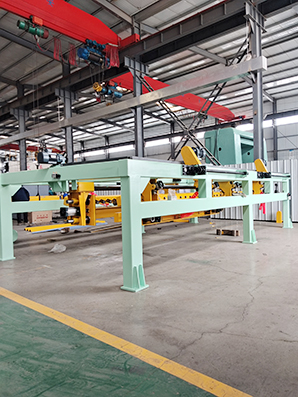
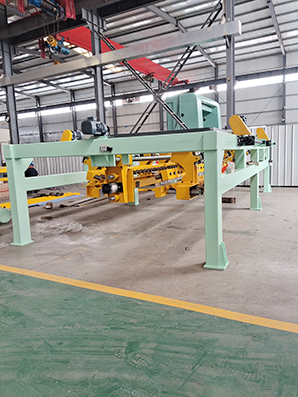